The Guardian: Two amputations a week: the cost of working in a US meat plant
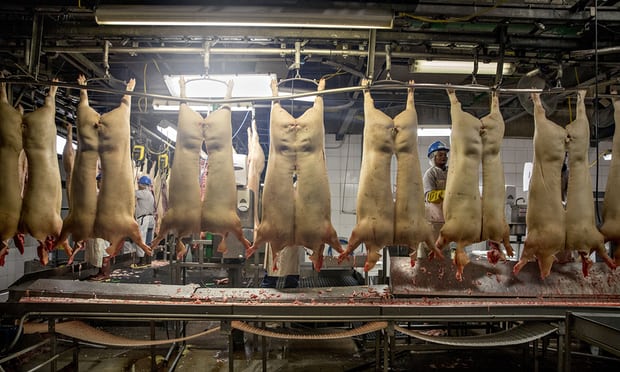
Pig carcasses in a midwest plant. US meat workers are three times more likely to suffer serious injury than the average American worker. Photograph: Daniel Acker/Bloomberg/Getty Images
by Andrew Wasley, Christopher D Cook and Natalie Jones | 5 Jul 2018
As unions warn of serious injuries, plans to take speed limits off the lines at pig plants are causing anxiety
Amputations, fractured fingers, second-degree burns and head trauma are just some of the serious injuries suffered by US meat plant workers every week, according to data seen by the Guardian and the Bureau of Investigative Journalism.
US meat workers are already three times more likely to suffer serious injury than the average American worker, and pork and beef workers nearly seven times more likely to suffer repetitive strain injuries. And some fear that plans to remove speed restrictions on pig processing lines – currently being debated by the government – will only make the work more difficult.
Government and industry bodies point out that there have been reductions in worker injury rates over the last couple of decades, although the figures still remain higher than average. They argue that despite the lifting of speed restrictions, the need to adhere to strict rules on food safety will impose its own limit on line speeds.
Records compiled by the Occupational Safety and Health Administration (OSHA) reveal that, on average, there are at least 17 “severe” incidents a month in US meat plants. These injuries are classified as those involving “hospitalisations, amputations or loss of an eye”.
Amputations happen on average twice a week, according to the data. There were 270 incidents in a 31-month period spanning 2015 to 2017, according to the OSHA figures. Most of the incidents involved the amputation of fingers or fingertips, but there were recordings of lost hands, arms or toes. During the period there were a total of 550 serious injuries which cover 22 of the 50 states so the true total for the USA would be substantially higher.
Recorded injuries include:
- An employee’s left arm had to be surgically amputated at the shoulder after it was pulled into the cubing machine during sanitation
- A worker was reaching down to pick up a box to clear a jam when his jacket became caught in a roller. As he tried to pull it out, his hand got pulled in as well. His hand and lower arm were crushed
- While an employee was attempting to remove the ribs from the spine of a cattle rib set, his hand made contact with a running vertical band saw and two of his fingers were amputated
- An employee working on a sanitation crew pushed the stop button after removing parts from the upper portion of a machine. The employee then placed his foot into a horizontal grinder while climbing down from the machine, causing all five toes on his right foot to be amputated
- A worker was clearing the hydrolyzer when back pressure caused hot feathers to discharge on to him. As he moved out of the way, he fell six feet, breaking a bone over his left eye and suffering first- and second-degree burns to the hands, arms, face and neck.
Chronic ailments are an even bigger issue, leaving many workers permanently disabled, and leading to losses and costs, both individually and publicly. According to one published study, carpal tunnel syndrome costs more than $2bn annually in medical treatment costs alone, for workers in all US industries.
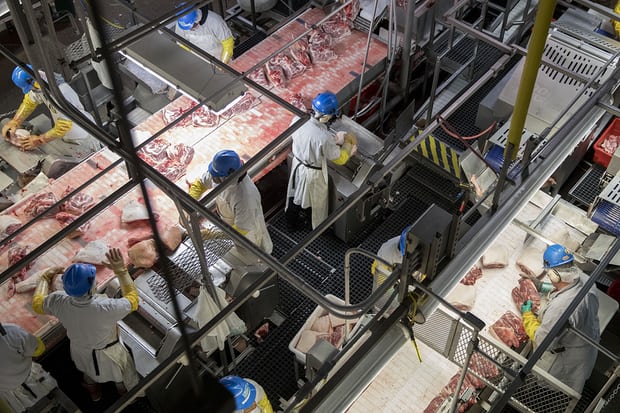
Campaigners fear plans to remove speed restrictions on pig processing lines – currently being debated by the government – will only make work more difficult. Photograph: Daniel Acker/Bloomberg/Getty Images
“Every co-worker I know has been injured at some point,” plant worker Eric Fuerstenberg told the USDA as they examined the case for implementing reforms that would include speeding up the line. “I can attest that the line speeds are already too fast to keep up with. Please, I am asking you not to increase them any more.”
A meat plant worker who asked to remain anonymous told the Guardian that although he has managed to avoid injury himself, most of his friends have needed surgery at some point. “If you complain about your hands, they just say you’ll be fine … they want you to put ice on it during your break time or lunchtime” – rather than during production hours.
The 50 year-old worker, from Nebraska, adds, “When I get home I have to stretch my hands, I feel a pinch, it hurts… You never get used to the work. I do it because I have to support my family. I don’t have an education.”
Amanda Hitt, from the Food Integrity Campaign, said: “Increased line speeds pose a real threat to workers. In addition to heinous injuries resulting from speed such as amputations and physical injury, workers are also at risk from injuries resulting from repeated motions. A pork plant worker may make … hard-cutting knife motions while working on a line. This repetition puts the worker at risk [of] debilitating musculoskeletal problems.”
However, official injury rates in the sector have been reduced over the last 25 years after an industry and government push to improve training and guidelines. “Worker safety is considered a non-competitive issue in the meat and poultry industry,” said Eric Mittenthal, spokesman for the North American Meat Institute (NAMI), “meaning companies openly share best practices with each other at meetings throughout the year, with the goal of making our facilities as safe as possible for the people working in them.”
Training has been increased, say industry bodies, and, in a joint effort with the unions, the government and industry, a set of voluntary ergonomic guidelines for the meat packing industry has been drawn up, described by OSHA as a model for other sectors. “And these efforts have really paid off,” said Mittenthal. “In 2016 we saw all-time lows for industry injury and illness rates.”
According to the most recent data published by the US Bureau of Labour Statistics “injury incidence in the meat and poultry packing and processing industries has decreased significantly over the past 25 years, reaching an all-time low of 5.3 cases per 100 full-time workers per year”. There remains, according to the Government Accountability Office, a persistent problem of under-reporting.
In 1994, according to BLS data, the incidence rate for injuries for meat packing plants was over 20. In the case of “lost workday injuries”, points out Mittenthal, the rate for animal slaughtering and processing was 3.8 cases per 100 workers versus 1.7 for “all industries including private state and local government”. A number of industries have higher rates than this.
However, some fear that aspects of a new system being piloted by the USDA may stall that progress. The New Swine Slaughter Inspection System (NSIS) will re-allocate some of the line inspection duties, and remove speed caps from the processing lines. USDA estimates that it could potentially save the agency more than $6m (£4.5m) a year.
But the plans will lead to more injuries, believe unions and workers. “When it’s production at all costs, people are going to get hurt,” said Mark Lauritsen, head of the meatpacking division for United Food and Commercial Workers (the main union for meat plant worker in the US). “There’s really no need for this, taking the caps off the line speed – there’s plenty of capacity to kill plenty of pigs … but they’re just getting greedy about it.”
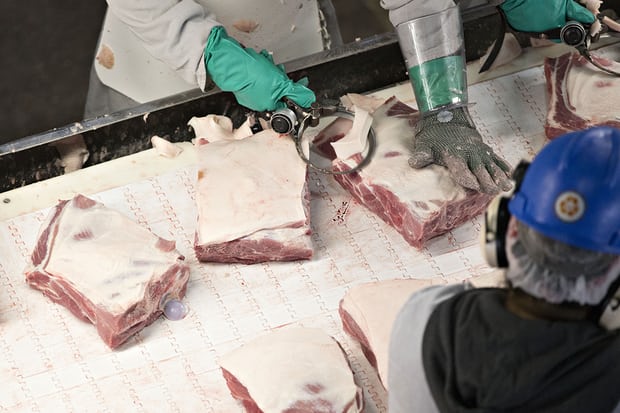
Employees trim fat from sections of pork at a US plant. Photograph: Daniel Acker/Bloomberg/Getty Images
“I am strongly opposed to any provision that would allow employers to increase the number of forceful repetitions workers are required to perform,” David Michaels, the former top OSHA administrator under President Obama, wrote in response to the plans. “The proposed rule allows employers to increase the line speed without adding additional workers. This will, without doubt, increase worker injuries and illnesses.”
But NAMI argues that the removal of line speed caps is not about speeding things up, but about allowing the line inspector to decide a speed that is appropriate for safety. Plants would not be capped at 1,106 pigs per hour, but they could only operate as fast as adhering to food safety rules would allow, said a NAMI spokesperson. In fact, under the pilot programmes that have been running, some plants actually ran more slowly than the current capped rate, they point out.
The USDA believes that the current inspection system forces vets to concentrate on areas that actually are not the priority for food safety concerns. They believe the NSIS will “improve animal welfare and compliance with the Humane Methods of Slaughter Act (HMSA); improve the effectiveness of swine slaughter inspection; make more efficient use of the agency’s resources; and remove unnecessary regulatory obstacles to innovation”.