Business Insider: ‘Entire aisles are empty’: Whole Foods employees reveal why stores are facing a crisis of food shortages
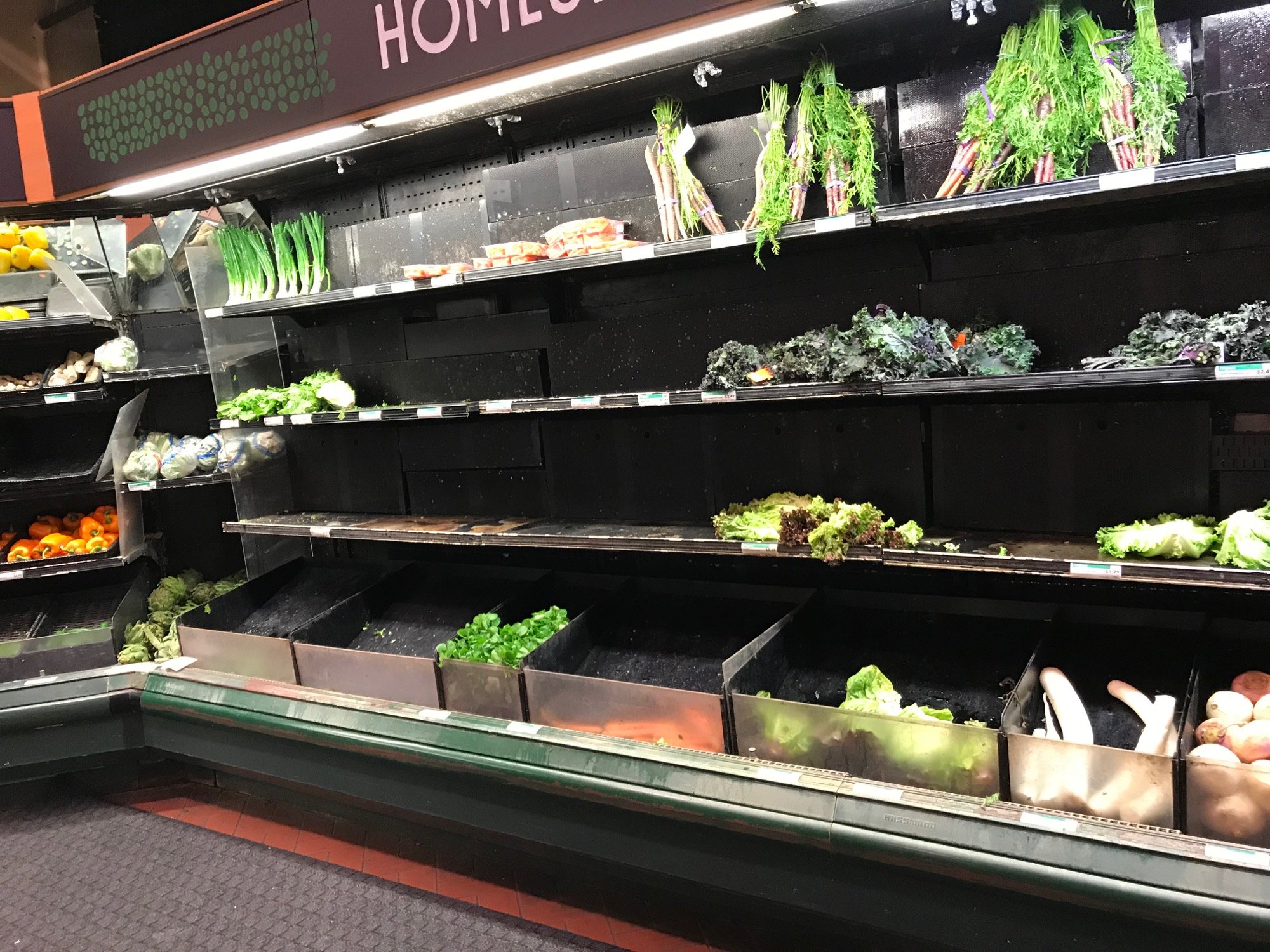
A Whole Foods store in Houston. Bettina Elias Siegel
by Hayley Peterson | Jan. 18, 2018
- Whole Foods employees say stores are suffering from food shortages because of a newly implemented inventory-management system called order-to-shelf, or OTS.
- Whole Foods says the system reduces unnecessary inventory, lowers costs, and frees up employees to focus on customer service.
- Employees acknowledge that less food is spoiling in storage rooms, but they describe OTS as a “militaristic” system that crushes morale and leads to many items being out of stock.
- “Last week, we ran out of onions and potatoes twice,” an employee of a Brooklyn Whole Foods store said. “Entire aisles are empty at times.”
- “It has for weeks had empty shelves, and I shop there twice a week,” one customer told Business Insider. “The prepared-food section is not refreshed, and food looks stale.”
Whole Foods is facing a crush of food shortages in stores that’s leading to empty shelves, furious customers, and frustrated employees.
Many customers are blaming Amazon, which bought Whole Foods in August for $13.7 billion. Analysts have speculated that the shortages could be due to a spike in shopper traffic in the wake of the acquisition.
But Whole Foods employees say the problems began before the acquisition. They blame the shortages on a buying system called order-to-shelf that Whole Foods implemented across its stores early last year.
Business Insider spoke with seven Whole Foods employees, from cashiers to department managers, who asked to remain anonymous for fear of retribution.
Order-to-shelf, or OTS, is a tightly controlled system designed to streamline and track product purchases, displays, storage, and sales. Under OTS, employees largely bypass stock rooms and carry products directly from delivery trucks to store shelves. It is meant to help Whole Foods cut costs, better manage inventory, reduce waste, and clear out storage.
But its strict procedures are leading to storewide stocking issues, according to several employees. Angry responses from customers are crushing morale, they say. (Many of the photographs in this story were provided to Business Insider by customers.)
“At my store, we are constantly running out of products in every department, including mine,” an assistant department manager of an Illinois Whole Foods told Business Insider. “Regional and upper store management know about this. We all know we are losing sales and pissing off customers. It’s not that we don’t care — we do. But our hands are tied.”
Whole Foods did not respond to several requests for comment on this story. The company’s executives have described the changes as cost-saving, and employees acknowledge that they have helped reduce food spoilage in stock rooms.
But even those who agree the company needed a better system to reduce losses and waste say it has gone too far.
How order-to-shelf is leading to food shortages
OTS operates under a strict set of requirements, mandated by Whole Foods’ corporate office in Austin, for purchasing, storing, and displaying products on store shelves, employees said.
One of those requirements, they say, has led to a dramatic reduction in Whole Foods stores’ so-called back stock, the products stored in back rooms until they are needed on store shelves.
“The system is now set up to pretty much only have enough product to keep the shelf full and no extra,” an employee of a store in Sacramento, California, told Business Insider. She said her department’s back-stock area was now 25% of the size it was before the implementation of OTS.
An employee of another store said the seafood department, which once had a giant freezer to store extra inventory, was now sharing one with the meat department.
“Last week, we ran out of onions and potatoes twice,” an employee of a Brooklyn Whole Foods store said. “Entire aisles are empty at times.”
A reduced back stock means that any unexpected increase in shopper demand or a product-shipment delay can result in out-of-stock items across every department, multiple employees said.
“If a truck breaks down and you don’t get a delivery, then you have empty shelves,” an assistant manager of a Chicago-area Whole Foods said.
An employee of a Texas Whole Foods store told Business Insider that stocking issues were “horrible” over the holidays and that the produce department “looked embarrassing.”
“I get constant and consistent complaints from customers for continuously being out of staple [products],” the Sacramento employee said. “It’s frustrating as an employee and also as a shopper.”
Employees say the system has ‘crushed’ morale
Whole Foods gets stores to comply with OTS by instructing managers to regularly walk through store aisles and storage rooms with checklists to make sure every item is in its right place and there is no excess stock. If anything is amiss, or if there is too much inventory in storage, the manager in charge of that area of the store is written up. After three write-ups, they can lose their job.
“Out of 400 boxes in your cooler, if you have one of those boxes facing the wrong way, you are penalized,” said one employee, who described the system as “militaristic.”
“It’s like taking a really high-stakes exam with 100 questions every day, and if you miss a single question you fail,” they added.
Multiple employees said these tests had “crushed” morale in stores because workers are terrified of getting “walked” and missing some small detail.
“You are so concerned about passing this military-like test that you actually start to lose your department’s operational conditions,” an employee said.
Another worker explained: “We think of it as punishment. They think of it as a way to correct errors.”
Whole Foods is streamlining food-buying to cut costs
OTS shifted some power from local buyers to Whole Foods’ corporate headquarters in Austin, which the company calls its global office, employees.
Before OTS, “buyers were more in control of what to bring in and how much to bring in,” a Whole Foods employee said. “Now everything is mandated at the global level, and while each store is different due to location and logistics, buyers must comply with the new system. This creates out-of-stocks, frustrations, and stress on all levels.”
Whole Foods has called it a cost-saving approach and says it has improved stocking issues.
“We’re moving basically from a federated system of purchasing to a unified system of purchasing, and we expect to see a lot of cost savings there,” Glenda Flanagan, a Whole Foods executive vice president, said on an earnings call in May.
The company has also said OTS frees up employees to focus on customer service.
Order-to-shelf “has transformed the inventory levels that we have in the back room, essentially clearing them out so that we’re mainly focusing on what we call our never-outs, the key items that we need to have in stock all the time in our stores,” Whole Foods’ vice president of operations, Ken Meyer, said on an earnings call in February. “So it’s creating a really strong, efficient process from the way the goods are received in the back door to bring them right out to the shelf. And it’s really improving and helping our out-of-stocks as well — dramatically.”
Every employee who spoke to Business Insider agreed that the system had been effective in reducing extra inventory. Stores’ back rooms and freezers that were once cluttered with unsold items — which could spoil before they were sold — are now nearly empty.
Multiple employees also said that before OTS, Whole Foods needed a more organized buying system.
“We had an outside company grade us on our inventory and our back stock” shortly before OTS’s implementation, one assistant department manager recalled. “We failed. We had millions of dollars in inventory just sitting around, hurting our bottom line.”
But now, the manager said, Whole Foods has gone to the opposite extreme.
“On paper, things look good — our spoilage is in check, and I don’t have a lot of back stock,” he said. “But I have never seen so many empty shelves in my store.”
Whole Foods workers are hoping Amazon will restock shelves
Some employees are hoping Amazon fixes Whole Foods’ out-of-stock problems.
“A lot of team members are hoping Amazon saves us, saying, ‘I can’t wait until Amazon learns how much money Whole Foods is losing with order-to-shelf,'” one employee said.
“You would think that with Amazon’s reputation for being a brutal employer that they would be behind the system,” he added. “But they are not. This is an entirely Whole Foods-driven problem.”
One employee at a Texas Whole Foods store said that when Amazon representatives at a recent question-and-answer session were asked about stocking issues, they indicated they weren’t aware of the problems and said they would have to be addressed with Whole Foods’ leadership.
Whole Foods said in May that accelerating its rollout of order-to-shelf had helped put the company on track to achieve $300 million in cost savings by 2020.
Some customers are turning away
Some Whole Foods customers who have noticed stocking problems say they are looking to shop elsewhere.
“My regular Whole Foods store is in Oxnard, California. It has for weeks had empty shelves, and I shop there twice a week,” Duane Palm told Business Insider. “The prepared-food section is not refreshed, and food looks stale. The bread is stale. Everything has turned downward since Amazon took over.”
“Something has gone terribly wrong with control and management at this store,” he added. “I found the same sad story at the Hillcrest store in San Diego.”
Patricia Brook said she found the same problems at a store in Fort Collins, Colorado, mentioning its stock of products from Whole Foods’ value brand, 365.
“No 365 cottage cheese, no 365 plain nonfat organic yogurt, no Brat Hans chicken breakfast sausage, no Norwegian salmon, no 365 brown eggs — shelves are bare!” she said. “So I come back once. Still bare! I come back twice. Still bare!”
She added: “Something has dramatically changed.”
Adrienne Elias said that she and her husband had for years been loyal to Whole Foods but that in the past year she had noticed constant out-of-stocks, poorly stocked shelves, and “limp, brown, soggy” produce.
“We found ourselves thrilled at the news that Amazon was assuming ownership, hoping that they would be able to fix the problems, a lot of which we believed to be the result of very incompetent staff,” she told Business Insider. “We thought that perhaps it would simply take more time.”
“Last week, after a totally frustrating shopping experience, we decided that they could not fix it or, most likely, they did not want to fix it,” she said. “Regretfully, we will begin shopping elsewhere.”